HPCI Green Pellet® is standardised, renewable, carbon neutral, biodiversity-friendly, and competitive with coal and oil.
It brings high economic and environmental value to the communities that use it. Second generation (2G) and protecting biodiversity, it uses lignocellulosic biomass residues (straws and husks, recycled and thinned wood, waste). It does not compete with food and livestock feed.
HPCI Green Pellet® is sanitized from microbes, viruses and bacteria that live in biomass.
It is cleaned of most heavy metals and chlorine. It does not emit CO during storage and produces little dust. Consequently, it avoids health risks (cancer, asphyxiation) and industrial risks (self-ignition, explosiveness).
Finally, it is inert and water resistant (hydrophobic) and does not ferment. It can be stored outdoors.
HPCI Green Pellet® reuses coal logistics equipment without adaptation. It offers high heat density and therefore competitive logistics.
With its high calorific value and density, and its high grindability, it can be used directly in coal boilers of all technologies (volcanoes, grate boilers, spreader-stokers, fluidised beds and pulverised boilers). It has a good combustion quality.
It is standardised and labelled by Européenne de Biomasse. HPCI Green Pellet® has identical characteristics regardless of the plant that produces it.
The market for HPCI Green Pellet® is therefore liquid and its price is competitive with coal plus the price of CO2.
HPCI Green Pellet® provides 2G bioethanol producers with consistent, high-quality supplies with excellent fermentability.
The co-products of ethanol production are valuable because our process does not use acids or additives. We produce no waste or liquid effluent during pre-treatment, and we consume less energy.
Our process is therefore competitive, 100% environmentally friendly and circular.
HPCI Green Pellet® provides a bio sourced, recyclable and 100% biodegradable raw material that is standardised, water-resistant and has a high adhesive strength (even after the pellets have been grinded). No chemical glues or materials that are harmful to health are used, differentiating us from synthetic panels.
Panels made from HPCI Green Pellet® perform well, particularly in the automotive, furniture and construction industries. HPCI Green Pellet® outperforms Isorel panels on all properties (thickness after swelling, perpendicular tension and flexural strength).
Producing HPCI Green Pellet® is possible thanks to our Edb-HPCI® technology:
- Edb-HPCI® is a breakthrough technology. It is the result of 10 years of research and development. It is protected by 18 patent families in 68 countries.
- It is defined as the continuous steam cracking of dry lignocellulosic biomass to produce, together or separately, biofuels, biomaterials, and biochemical products
- It is meant to be compatible with all types of steam crackers, pelletizers, and dryers on the market
- It produces no waste and has a material yield of 100%. It does not use any chemical additives

- The biomass residues are introduced for a few minutes into a highly pressurised reactor
- The pressure is suddenly released to atmospheric pressure
- The volume occupied by the water molecules increases, which grinds the material
- Increasing temperature changes the structure of lignin, cellulose and hemicellulose molecules
- The continuity of the process enables the separation of particles and gases
- The gases are recovered in biochemistry or bioenergy
- The solid particles are packaged in HPCI Green Pellets®.
FICAP, a world first
We built the world's first plant capable of producing HPCI Green Pellet® to prove that this advanced pellet, which replaces coal and oil, can be produced on an industrial scale.
Designed and developed by Européenne de Biomasse, FICAP is a 125,000 tonnes per year HPCI Green Pellet® plant financed (€50M) by our partners Meridiam and Banque des Territoires.
FICAP is a model of industrial ecology: 100% material yield, so zero waste, little noise, no smoke and no water consumption.
FICAP has created 350 direct jobs in the local industry and offsets the annual CO2 emissions of 230,000 cars.
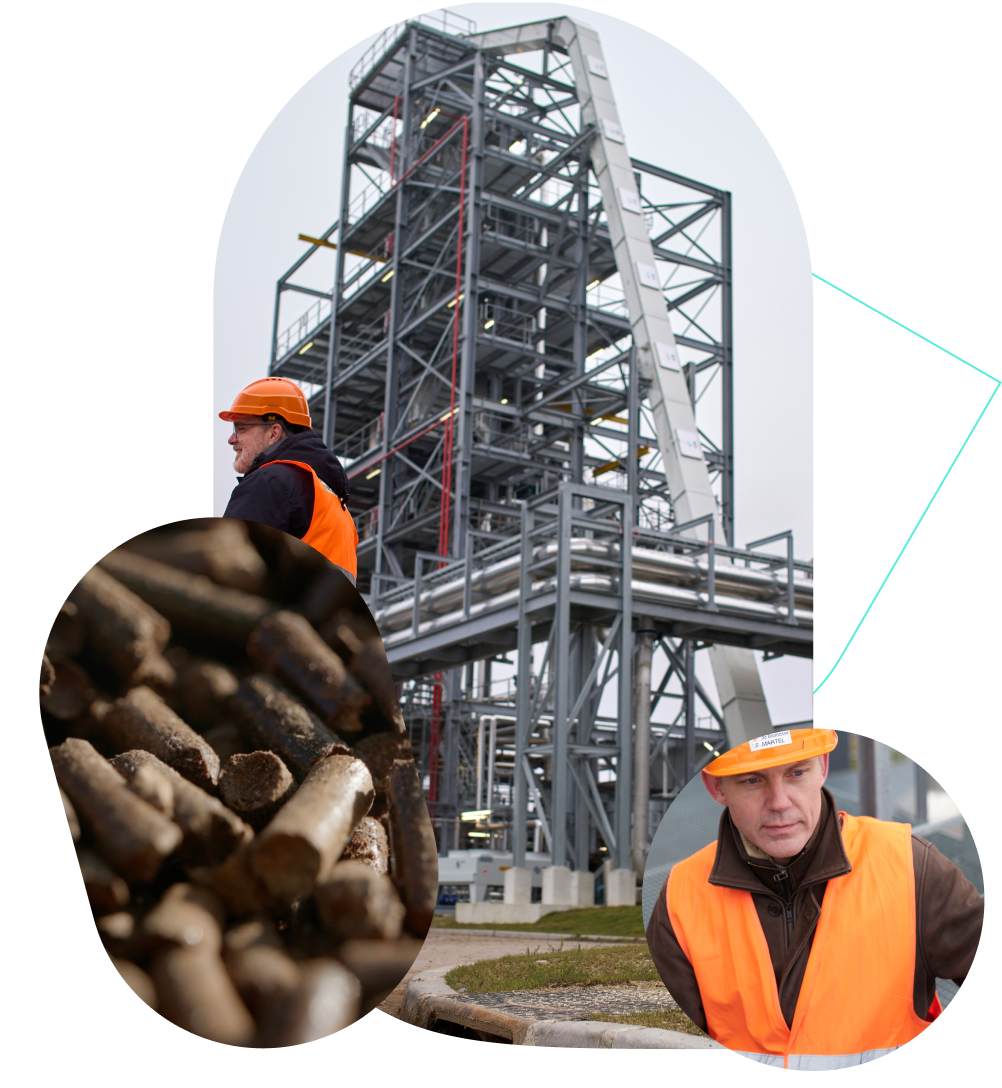
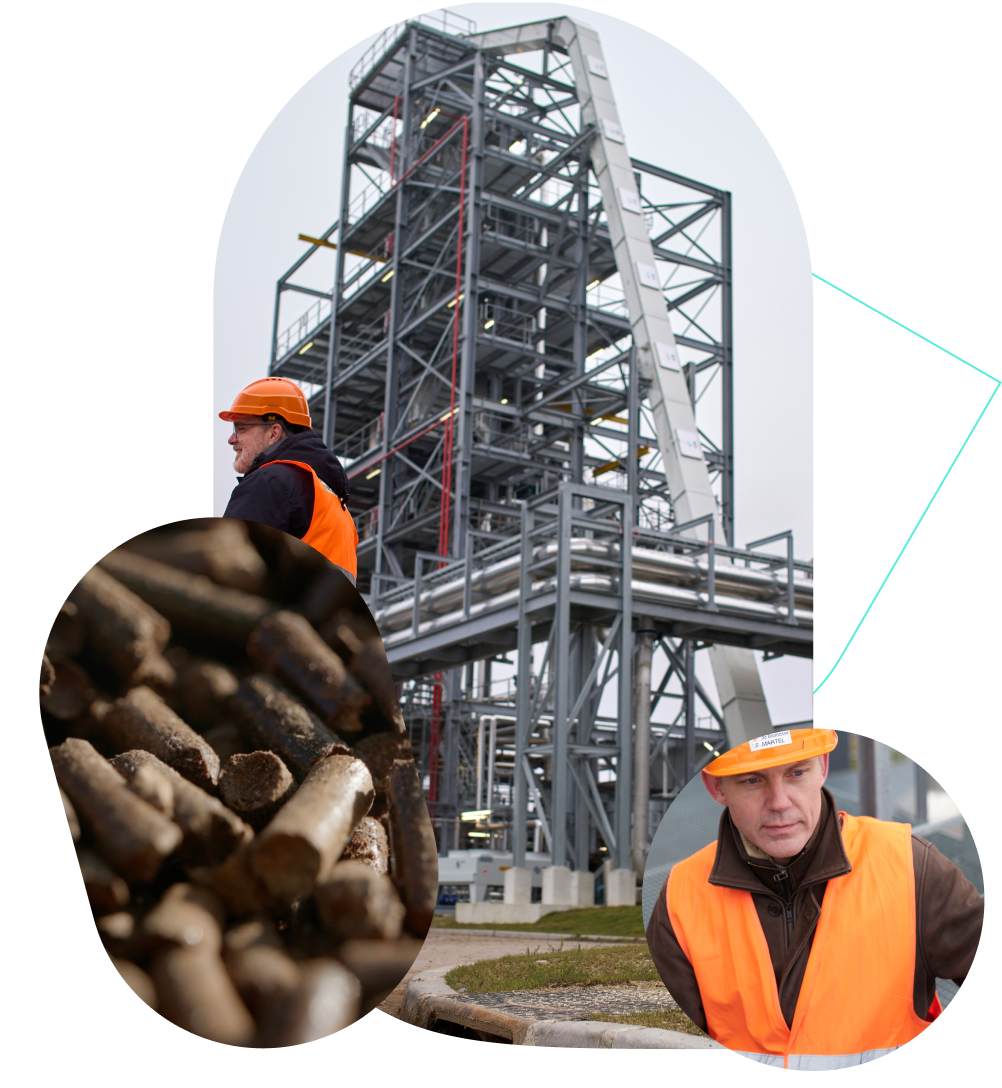
FICAP, a world first
We built the world's first plant capable of producing HPCI Green Pellet® to prove that this advanced pellet, which replaces coal and oil, can be produced on an industrial scale.
Designed and developed by Européenne de Biomasse, FICAP is a 125,000 tonnes per year HPCI Green Pellet® plant financed (€50M) by our partners Meridiam and Banque des Territoires.
FICAP is a model of industrial ecology: 100% material yield, so zero waste, little noise, no smoke and no water consumption.
FICAP has created 350 direct jobs in the local industry and offsets the annual CO2 emissions of 230,000 cars.
Testimony of an industrialist
"I have invested in Européenne de Biomasse because I have full confidence in the management team to successfully create a groundbreaking technology and implement it on a global scale. (...) "
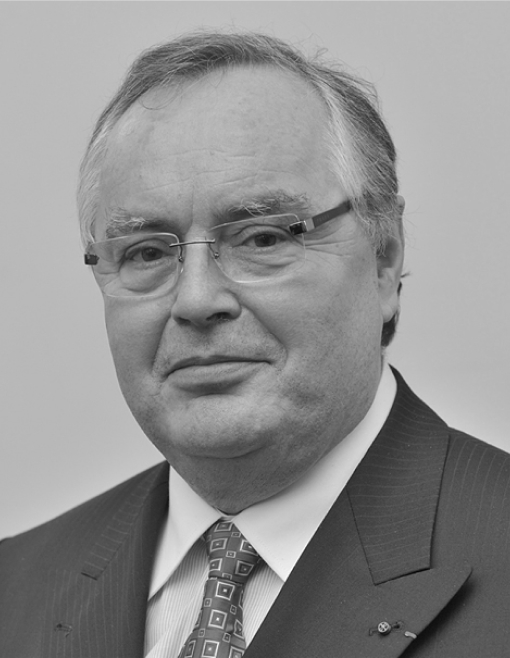
Roland Vardanega former Chairman of the Board of Directors of the PSA GrouP
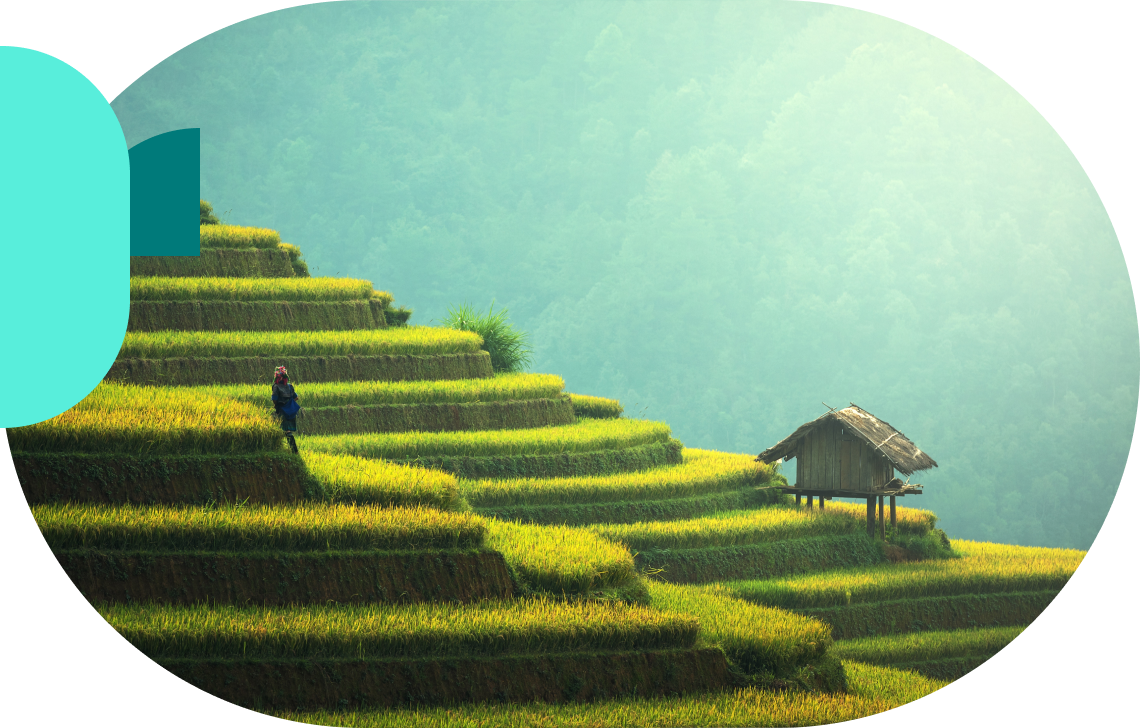
Our contribution to the environment
The manufacture of HPCI Green Pellet® is financially viable, environmentally friendly and creates sustainable jobs. HPCI Green Pellet® meets all the conditions to replace fossil energies and decarbonise the planet.
Interested in finding out more?
For more detailed documentation, please contact us.